Scientists develop system to produce biodegradable plastics
A team of scientists has developed a system that uses carbon dioxide, CO2, to produce biodegradable plastics, or bioplastics, that could replace the nondegradable plastics used today. Read more on Dynamite News:
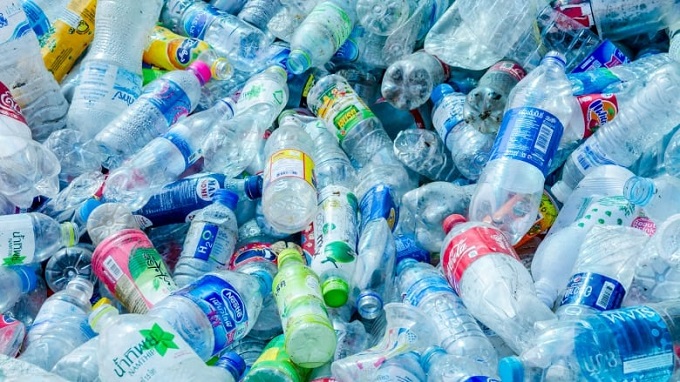
Washington [US]: A team of scientists has developed a system that uses carbon dioxide, CO2, to produce biodegradable plastics, or bioplastics, that could replace the nondegradable plastics used today. The research addresses two challenges: the accumulation of nondegradable plastics and the remediation of greenhouse gas emissions.
Published Sept. 28 in Chem, the research was a collaboration of Susie Dai, Ph.D., associate professor in the Texas A&M Department of Plant Pathology and Microbiology, and Joshua Yuan, Ph.D., formerly with the Texas A&M Department of Plant Pathology and Microbiology as chair for synthetic biology and renewable products and now Lopata professor and chair in the Washington University in St. Louis Department of Energy, Environmental and Chemical Engineering.
Read also: Health: Gut bacteria may contribute to HIV infection susceptibility: Study
The research was made possible by the John '90 and Sally '92 Hood Fund for Sustainability and Renewable Products, Texas A&M AgriLife and Texas A&M University. Dai said today's petroleum-based plastics do not degrade easily and create a massive issue in the ecosystems and, ultimately, oceans.
To address these issues, the Texas A&M College of Agriculture and Life Sciences researchers and their teams worked for almost two years to develop an integrated system that uses CO2 as a feedstock for bacteria to grow in a nutrient solution and produce bioplastics.
Also Read |
Relationships with colleagues more likely to develop in winters
Peng Zhang, Ph.D., postdoctoral research associate, and Kainan Chen, doctoral student, both in the Texas A&M Department of Plant Pathology and Microbiology, contributed to the work. The Texas A&M University System has filed a patent application for the integrated system.
"Carbon dioxide has been used in concert with bacteria to produce many chemicals, including bioplastics, but this design produces a highly efficient, smooth flow through our carbon dioxide-to-bioplastics pipeline," Dai said.
"In theory, it is kind of like a train with units connected to each other," Dai said. "The first unit uses electricity to convert the carbon dioxide to ethanol and other two-carbon molecules -- a process called electrocatalysis. In the second unit, the bacteria consume the ethanol and carbon molecules to become a machine to produce bioplastics, which are different from petroleum-based plastic polymers that are harder to degrade."
Using CO2 in the process could also help reduce greenhouse gas emissions. Many manufacturing processes emit CO2 as a waste product. "If we can capture the waste carbon dioxide, we reduce greenhouse gas emission and can use it as a feedstock to produce something," Dai said. "This new platform has great potential to address sustainability challenges and transform the future design of carbon dioxide reduction."
The major strength of the new platform is a much faster reaction rate than photosynthesis and higher energy efficiency. "We are expanding the capacity of this platform to broad product areas such as fuels, commodity chemicals and diverse materials," Dai said. "The study demonstrated the blueprint for 'decarbonized biomanufacturing' that could transform our manufacturing sector."
Also Read |
World's first male contraceptive gel comes closer to reality
Read also: Health: Researchers find immunotherapies for chemotherapy-resistant breast tumour
Dai said currently, bioplastics are more expensive than petroleum-based plastics. But if the technology is successful enough to produce bioplastics at an economic scale, industries could replace traditional plastic products with ones that have fewer negative environmental impacts. In addition, mitigating CO2 emissions from energy sectors such as gas and electric facilities would also be a benefit.
"This innovation opens the door for new products if the bacterium is engineered to consume carbon dioxide-derived molecules and produce target products," Dai said. "One of the advantages of this design is the condition the bacteria grow in is mild and adaptable to industry-scale conditions." (ANI)